Table of Contents
Economic feasibility of Passive House design
1 Economic feasibility of Passive House Design and corresponding renovation bundles
To evaluate the economic feasibility of Passive House Design in general all relevant cost data have to be accounted for. The idea behind the conception of energy efficient building design is to reduce energy consumption costs (and other annual expenses e.g. for maintenance) during lifetime of the building significantly. But to get the savings, some extra investment has to be done when doing the renovation or new built construction. The energy-cost savings then can be used to finance the extra investment cost which are probably needed to get better building components to form the energy efficient building envelope:
- more and better thermal insulation layer
- windows with low U-value < 0.85 W/m²K
- ventilation system with heat recovery
- …
To compare energy cost savings with extra investment costs both cost categories have to be re-calculated via dynamic finance calculation methods: annual expenses must be transformed to present cash value or vice versa. In doing so the reduced energy costs and the relevant investment costs, respectively – see figure 1 for several variants of renovation a building – can be added up easily.
The reduced energy costs can be calculated easily with energy balance calculation tools such as PHPP for each setup for renovation or new built, respectively. To do so PHPP has been accomplished with a financial calculation tool (PHeco), which performs the recalculation of annual expenses to present cash values and gives some table structure to organize cost data input.
For any special renovation action or new built construction, the economic feasibility can now be evaluated easily by comparing the full height of the stacked columns in the figure 1: extra investment costs will reduce the energy costs for each setup respectively.
Several renovation projects have been evaluated with this method and could show good results.
2 New built single family & apartment building
2.2 New built single family row-house building: PH compared with low energy building
This example is to update cost evaluation on the basis of realized projects. This single family row-house building was erected in 2007/2008. In total nine dwelling units were realized at the same time with one construction team formed by the architect as a general planner and several smaller craftsmen companies: carpenter, window manufacturer and installer, plumber, electricians,…. see, figure 2.
Construction: Cellar with concrete bottom slab as flat foundation with XPS insulation layer beneath, so cellar is within the warm envelope. Construction above ground: lightweight wooden prefabricated elements, see table in figure 2. Invoiced construction costs for the whole PH building were about 1200 €/m² (cost group 300 building envelope and cost group 400 building service). The costs for energy saving components are reported in detail below.
The Passive House buildings all have a mechanical ventilation system with heat recovery. To compare cost of LEB an exhaust air ventilation system with one fan, silencers and outside air inlets in walls was accounted for, as this is required in Germany since 2009 to provide sufficient (hygienic) continuous air change. For all other configuration features see in table in figure 2.
The costs of all components relevant for energy savings are accounted for in this section. So not only building envelope components, but also building service components are included: cost of ventilation and heating system are fully accounted for. Accordingly in this section the final energy demand for the heating system including heat distribution losses and including auxiliary electricity for ventilation and heating system was used to calculate energy costs. This approach is used in PHPP9 and PHeco in general, as this allows to fully account for the real situation of the user and investor: all costs have to be accounted for and are to be compared.
2.3 Cost data assessment
Cost data for the Passive House buildings were available as the project was realized with the architect (Georg Zielke, Darmstadt) as general planner, who did planning and negotiation with companies. But all families (investors) had single contracts with the construction team companies: craftsmen and suppliers of components. This is an advantage with respect to cost transparency, but has some risk, e.g. rising construction costs during planning as the responsibility for contracts lies solely with the investing family. The fact that one single construction team was doing all nine building units provided the chance to get good prices, as serial effects could be used. For economic analysis accounted costs were available for all the passive house buildings. The costs coming out of the invoicing are sorted by components and energy saving actions, see figure 3, such as:
- air tightness
- thermal insulation of cellar, bottom slab, outside wall, roof
- windows, entrance door, shading
- heating system
- ventilation system
To compare the costs of several components specific cost values in €/m² were calculated. The area used is the same treated floor area, which is used in PHPP to do energy balance calculations. So cost data for investment and energy consumption can easily and directly be compared.
In Figure 3 mainly energy saving components are listed. The only exception are the shading which is the same for PH and LEB, but is needed to keep the building well tempered (passive cooling) in summer. Cooling in summer is not accounted in this section, because in Germany and Central Europe active cooling systems are usually not necessary and not commonly used. Therefore no energy costs or savings for (active) cooling are accounted for. In PHPP 9 active cooling can be covered if necessary.
For the basic version of PH the costs for energy saving components are in total 322 €/m² TFA. This value is compatible with the experience from other projects.
Cost estimation for LEB. For this project no comparable LEB was available to get invoiced cost data. Therefore costs were estimated according to data from literature: less insulation thickness, no expenses for air-tightness, simple exhaust air ventilation system reduce the costs for the LEB. On the other hand the connection to district heating needs a higher maximum power (15 kW instead of 6 kW). The costs for the connection are rated directly with the maximum power. In addition the LEB has higher costs for heating system as each room has a radiator, whilst in PH one single air heater is used, radiators only in bathrooms.
The sum of costs for energy saving components for the LEB are therefore only about 240 €/m² TFA and thus the difference to PH is 82 €/m². The relative extra expenses for PH components from these numbers are about 8 % which is in line with earlier PH projects.
2.4 PH are economically reasonable,
but optimization of building envelope is important
PH components as described above are economically reasonable with present boundary conditions, see table 4. So the higher investment costs are paid back by reduced energy consumption costs during lifetime of the building. Therefore the documentation of 'total lifecycle costs' is important to give a transparent view of the facts.
Two effects have to be pointed out here:
- it is worth while to optimize all components to the cost optimum. Having rather high energy prices this intends to reduce energy costs and have some more investments in corresponding energy saving components.
- The numbers of cost data out of the study shown in this section are by intention taken from a 'cost effective' basic version of a building. This intends as well the selection of materials. So PVC window frames are used in PH and LEB. Extra costs for wooden or wood-aluminum are not accounted for. Using these would result in extra costs for both, PH an LEB. It is important to always compare apples with apples!
- Windows have cost reduction potential
- Ventilation systems have cost reduction potential.
Using all the above mentioned numbers and calculating present values from all cost categories results in the total costs for PH and LEB shown in figure 3. Summary and outlook: Lower interest rates get the capital cost reduced and higher energy prices will lead to higher savings. So the present situation favors investment in energy efficiency components for buildings.
interest rate *) | 2.5 % | real interest rate (without inflation) |
period of consideration | 20 a | with constant interest rate |
lifetime of components | 30 a | building service: ventilation with heat recovery, radiators (average value) |
“ | 30 a | windows |
” | 50 a | termal insulation of wall, roof, cellar |
price for final energy *) | 0.10 €/kWh | gross, district heating (2008, typical value) |
price for electricity *) | 0.22 €/kWh | final energy |
Table 2: Basic assumptions for dynamical cost calculation for row house 2008. Also see [Kah/Feist 2008] (*) Energy price and interest rate in 2008.
3 Cost effective deep energy renovation
In the same manner as above for the new built single family home some renovation projects were analyzed within the framework of IEA Annex 61 '… deep energy renovation' [IEA 61]. The energy costs can be reduced significantly by adding thermal insulation and ventilation with heat recovery, better air-tightness and less thermal bridges, etc. Several bundles of these energy saving components are set up see table 3 to look for the overall lifecycle cost of each bundle. Form that it can be decided easily which setup or bundle is to be preferred economically.
1-status quo (old building |
2-EnEV 140 50%-savings ─ cost optimized |
5-EnEV cost optimized PVC windows |
6-PH1 as realized, timber aluminum window frames |
7-PH2 cost optimized windows cost optimized ventilation system |
Table 3: School building – renovation with PH-components (2013). Short description of renovation 'bundles' or variants – variant No 6 was realized.
In many cases the concern of investors is reduced to the question to have the cheapest investment done to just fulfill the legal requirements with respect to energy savings. This is the bundle No 5 (EnEV) in the following graphs. But it turns out that this point of view is often misleading: better components which might be more expensive will have higher energy savings and thus will lead to lower energy costs during life time.
In figure 5 the final energy demand of each bundle is shown to display that every action has a significant impact on energy use of the building. In figure 6 vice versa the extra investment costs for energy saving actions are shown for each bundle in detail. From that it can be seen easily which components have further cost reduction potential: this is mainly the windows and the ventilation system. For windows cost reduction could already be realized as meanwhile (2015) windows with PH quality are available for about the same costs as formerly 'standard' EnEV windows with less insulation and only two pane glazings. Ventilation systems have to be revised with that respect in the near future. As it can be seen from figure 6 bundle No 7 (PH2 cost optimized) − the cost for ventilation systems should come down to about 80 €/m² TFA instead of 160 €/m² TFA.
In figure 7 the sum of all cost categories shows the total life cycle costs of various bundles of energy saving actions for this building. Within the accuracy of the calculations ─ error bars for energy costs and investment costs are indicated in the graphs ─ the total life cycle costs for bundle No 5 (EnEV, German building code) and No 7 (PH2 cost optimized PH components) is roughly the same but No 7 is slightly lower.
In addition it turns out that already the more expensive bundle No 6 (PH1 as realized) comes with equal total lifecycle costs as the status quo − old building before renovation with high energy costs.
Conclusion: it turns out clearly, that using cost optimized but good quality PH components which are to be developed consequently during the next few years, give potential to realize cost effective 'deep energy renovation' projects. Cost effective is said in this context with respect to total life cycle costs. The same is true for new built as well.
This fact is crucial for so called contracting business models, which are to be developed within IEA Annex 61 [IEA61]: a contractor must be sure, that in the end the overall lifecycle cost – investment, energy, maintenance – will be as low as calculated before. If energy prices would increase, the risk of higher total costs will be higher for the 'low investment cost bundle'. So the concern of investors has to be redirected from the narrow view of pure short time investment costs to the wider view of total life cycle costs.
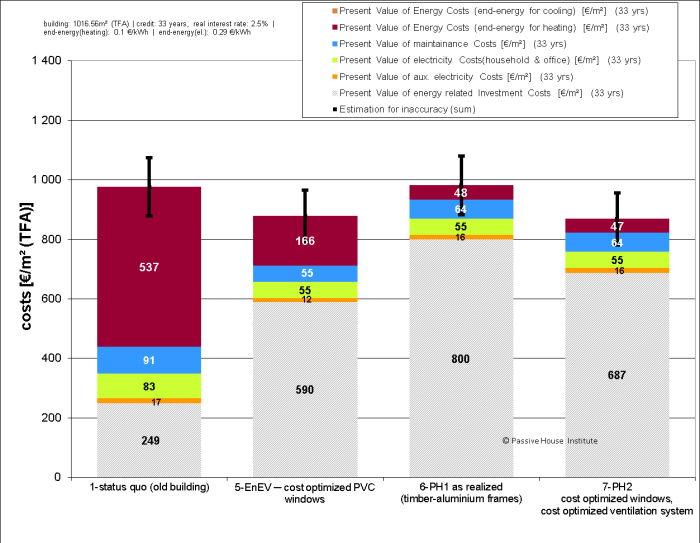
4 Literature
[AKKP 11] Feist, W. (Hrsg.), Kostengünstige Passivhäuser. Protokollband Nr. 11, Arbeitskreis kostengünstige Passivhäuser Phase I, Darmstadt 1997.
[AKKP42] Feist, W. (editor), Ökonomische Bewertung von Energieeffizienzmaßnahmen, Protokollband Nr. 42, Arbeitskreis kostengünstige Passivhäuser Phase V, Darmstadt 2011.
[IEA 61] Business and Technical Concepts for Deep Energy Retrofits in Public Buildings, www.iea-annex61.org Part of the data evaluation was done within this framework and financed by German Government: Bundesministerium für Wirtschaft und Technologie (BMWi).
[Kah/Ebel/Peper/Feist 2010] Kah, O., Ebel, W., Peper, S., Feist, W., Untersuchung zum Außenluftwechsel und zur Luftqualität in sanierten Wohnungen mit konventioneller Fensterlüftung und mit kontrollierter Lüftung, Forschungsbericht im Rahmen des IEA Task 37, gefördert vom Bundesministerium für Wirtschaft und Technologie, Passivhaus Institut, Darmstadt, 2010.
[Kah/Feist 2008] Kah, Oliver; Feist, Dr. Wolfgang; Pfluger, Dr. Rainer; Schnieders, Jürgen; Kaufmann, Dr. Berthold, Schulz, Tanja; Bastian, Zeno: Bewertung energetischer Anforderungen im Lichte steigender Energiepreise für die EnEV und die KfW-Förderung, Hg. von BMVBS / BBR, BBR-Online-Publikation 18/2008. urn:nbn:de:0093-ON1808R222
[Kaufmann/Ebel/Feist 2010] Kaufmann, B, Ebel, W. Feist., W, Ökonomische Evaluierung zweier Sanierungsprojekte mit Dokumentation der abgerechneten Kosten: Hoheloogstraße und Schlesierstraße in Ludwigshafen, Forschungsbericht IEA Task 37, gefördert vom Bundesministerium für Wirtschaft und Technologie, Passivhaus Institut, Darmstadt, 2010.
[Kaufmann/Ebel 2010]: Kaufmann, B., W. Ebel, Economics of high thermal performance
old house renovation projects, Beitrag zum englischsprachigen Handbuch “Advances in Housing Renovation” im Rahmen von IEA Task 37, gefördert vom Bundesministerium für Wirtschaft und Technologie BMWi. Passivhaus Institut, Darmstadt, 2010
[Peper/Feist 2009] Peper, Dipl.-Ing. Søren; Feist, Wolfgang: Gebäudesanierung “Passivhaus im Bestand“ in Ludwigshafen / Mundenheim, Messung und Beurteilung der energetischen Sanierungserfolge, Darmstadt, 2009. Im Auftrag der GAG Ludwigshafen, Download unter: www.passiv.de
[Schöberl/Hutter 2003] Schöberl, H., Hutter, S., et al., Anwendung der Passivhaustechnologie im sozialen Wohnbau, Projektbericht im Rahmen der Programmlinie 'Haus der Zukunft', Bundesministerium für Verkehr, Innovation, Technologie, Wien 2003
Acknowledgements: Part of this work was financed by German Government: Bundesministerium für Wirtschaft und Technologie (BMWi) in the framework of
- IEA Task37 “Advanced Housing Renovation with Solar & Conservation” and in the framework of
- IEA Annex 61 “Business and Technical Concepts for Deep Energy Retrofits in Public Buildings” and by
- Deutsche Bundesstiftung Umwelt and supporters of “Arbeitskreis Kostengünstige Passivhäuser, V” [AKKP42].
The sole responsibility for the content of Passipedia lies with the authors. While certain marked articles have been created with the support of the EU, they do not necessarily reflect the opinion of the European Union; Neither the EACI nor the European Commission are responsible for any use that may be made of the information contained therein. |